판금사업 개척의 동행자가 되어준 살바니니
"디포르마씨오네(Deformazione)" 2022년 5월호
2007년에 설립된 다켄(Daken)사는 상업용 및 산업용 차량 플라스틱 액세서리 생산을 전문으로 합니다. 그리고 2020년, 판금 액세서리를 라인에 포함하면서 새로운 시장을 개척하기로 결정하였습니다.
우리는 이탈리아 마테라(Matera)지역의 생산현장을 방문하여 시장 진출 과정에서 살바니니를 파트너로 선정한 이유를 확인해 보았습니다.
다켄의 창립자이자 CEO인 "주세페 로루소( Giuseppe Lorusso)"씨를 인터뷰 해 보았습니다.

▶Daken사에 대해 소개 부탁드립니다.
다켄은 90명 이상의 직원을 보유한 회사입니다. 주로 도구상자나 차량 아래에 배치되는 플라스틱 소화기 캐비닛을 생산하는데, 그 덕분에 계속해서 시장을 장악해 왔습니다.
우리는 사출 성형용 폴리프로필렌 부분의 시장 리더입니다. 주로 유럽 전역에 지사를 두고 있지만 호주에서 싱가포르, 남아프리카에서 미국에 이르기까지 72개국에 서비스를 제공하고 있습니다.
스칸디나비아, 미국, 캐나다, 그리고 호주와 같은 일부 국가에서는 꾸준히 철강이 선호되고 있습니다. 그렇기 때문에 판금제품의 시장은 성장 가능성이 무궁무진합니다.
우리는 이미 수 년 동안 사출성형 분야에서 경험을 쌓아왔고, 시장과 유통업체에 대한 지식 또한 이미 가지고 있기에, 새로운 제품일지라도 상업적 측면에서 진입 비용에 대한 부담 없이 통합할 수 있었습니다.
▶기존의 플라스틱 사업과 차이점이 있나요?
네. 사실 기존의 우리 사업인 플라스틱의 생산 공정은 철강 공정보다 훨씬 간단합니다.
색상이나 스티커 등 몇 가지 세부사항을 지정할 수는 있지만, 표준 제품이 정해져 있고, 맞춤 생산이 불가하기 때문입니다.
하지만 판금사업은 다릅니다.
주문이 들어온다고 해서 모든 기계가 작동하는 것은 아닙니다. 효율성을 높이고 틀 교체 횟수를 줄이기 위해 고객 주문에 가장 적합한 방식을 모색합니다.
생산을 계획할 때 주문, 주문 내역, 그리고 사용 가능한 창고의 크기와 같은 몇 가지 요소를 고려합니다. 주문을 받으면, 구성 요소의 사용 가능성에 따라 조립 및 배송 계획을 정리하고, 이 단계에서 필요한 사소한 고객 주문사항도 해결합니다.
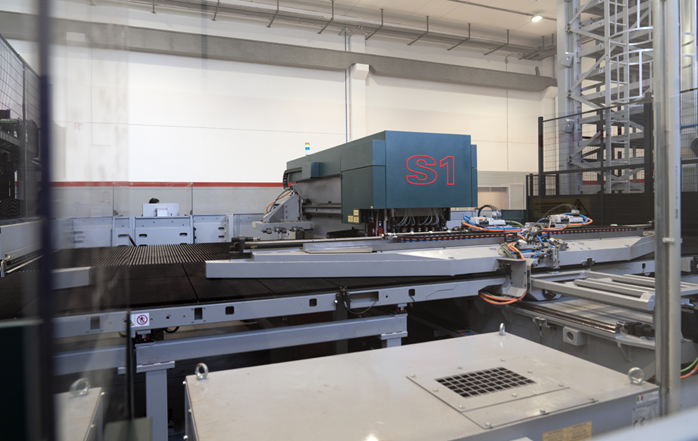
▶다켄이 선택한 라인은 무엇인가요?
기존의 플라스틱 생산 전략은 높은 수준의 맞춤화를 필요로하는 판금 요구사항을 충족시키기 어려웠습니다. 완전히 다른 생산 시스템을 선택해야 했기 때문입니다.
회사는 고객에게 맞춤형 솔루션을 제공함과 동시에 프로세스를 최적화하는데 도움이 될 수 있는 유연한 기술을 찾았고, 살바니니의 유연생산 시스템이 선택되었습니다.
생산라인은 S1 펀치-레이저 기계와 연결된 2개의 MD 자동창고로부터 시작됩니다. 이 창고는 30층으로 구성되어 있으며, 높은 수준의 라인 자율성과 유연성이 특징입니다.
S1은 펀치와 레이저 절단이 가능한 펀치-레이저 콤비 기계입니다. 한 단계에서 다양한 공정을 처리하고, 작업자의 개입도 없어서 생산 공정을 최적화하고 낭비를 줄여줍니다.
S1 다음의 MCU 자동 분류 장치는 펀칭 및 절단이 완료된 반제품을 적절한 장소로 보내줍니다. 쌓아 뒀다가 용접 또는 도장구역으로 보내주기도 하고, 절곡이 필요한 경우 자동적으로 P4 자동 절곡기로 보내지기도 합니다.
다켄이 선택한 P4 자동 절곡기는 최대 길이 2200mm, 높이 254mm까지 철판을 구부릴 수 있으며 위쪽 또는 아래쪽에 보조 칼날인 CLA도구가 장착되어 있습니다. 자동 절곡기에 연결되어 있는 롤러 컨베이어는 라인의 마지막 장비입니다.
일정한 반복성을 가지는 표준 제품을 만드는 것과, 주문에 따라 맞춤형 제품을 생산하는 것은 완전히 다른 것입니다. 그렇기에 우리는 살바니니에게 매우 유연한 라인을 요청했습니다. 그것이 우리 시장에서 판금 제품을 통합하기 위한 핵심이었기 때문입니다.
▶생산 방식에 있어서도 차이가 생겼나요?
네. 우리는 기존의 장기계획을 세우던 방식이 아닌 2주 정도의 계획을 설정합니다. 주문에 따라서 설계도와 도면에 따라 제작할 부품을 파악하고, 원자재 수급 여부를 확인하고 생산을 시작합니다.
오늘날 우리의 전략은 적시에 이루어지는 것이며, 이를 통해서 창고에 엄청난 양의 반제품을 비축하지 않고도 표준 제품과 맞춤형 제품을 효율적으로 관리할 수 있게 되었습니다.
그리고 이 모든 과정은 살바니니의 OPS 소프트웨어에 의해 수행됩니다. 이것은 고급의 생산 논리 및 과정을 단순화해줍니다.
3D도면으로 제품을 설계할 때 엔지니어링 부서에서는 STREAM을 사용하는데, 우리는 프로그램을 기계에 보내고 그걸로 끝입니다.
과거에는 다른 그 누구도 우리에게 이러한 통합 소프트웨어를 제공한 적이 없습니다. 다양한 기술이 서로 상호작용하지 않기 때문에 우리는 펀칭기용, 자동 절곡기용, 수동 절곡기 용 프로그램을 각각 실행해야 했습니다.

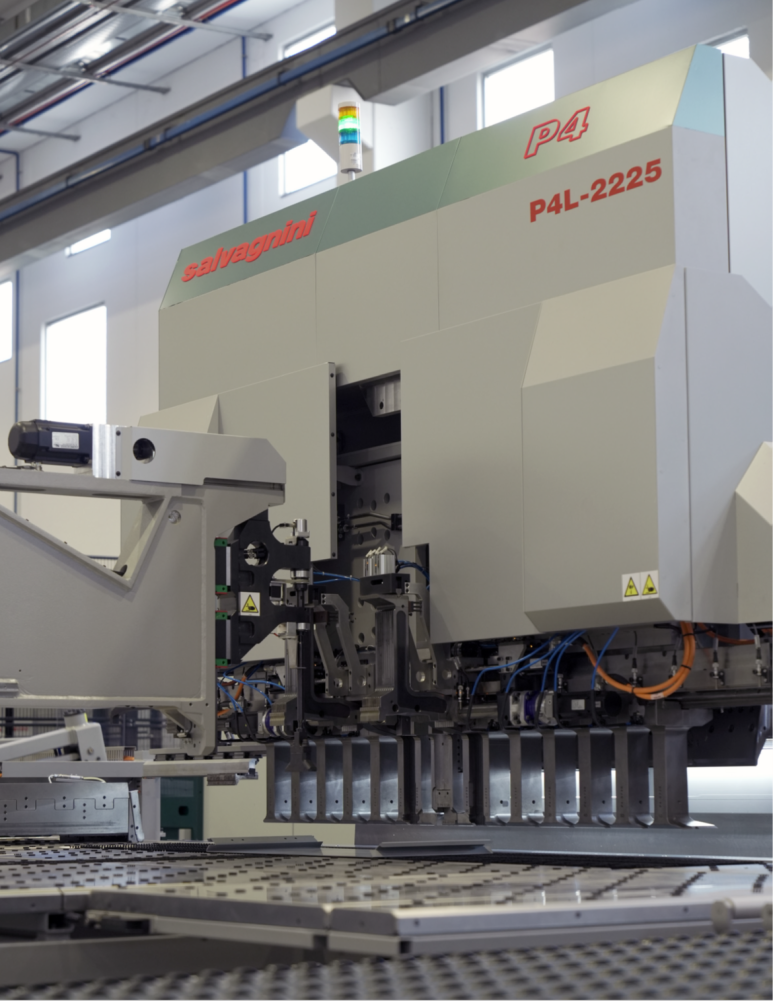
▶사업 확장에 있어서 가장 신경쓰는 부분이 무엇인가요?
이 사업에 있어서 가장 기본이 되는 것은 제품을 지속적으로 개선하고 더 나은 서비스를 제공하는데 도움이 되는 생산 기술을 보유하는 것 입니다.
이것이 우리가 생산 시스템에 투자하고 모든 구성요소를 사내에서 생산하는 이유입니다.
처음 판금 생산을 시작했을 때인 2020년 부터 전문 직원을 채용하기 시작하여 현재는 90명이 넘는 직원들이 일하고 있습니다. 그렇기에 직원 교육에도 더욱 집중하고 있습니다.
기술과 노하우는 또한 제품에 영향을 미칩니다. 이것은 우리 직원들에게 다양한 분야 및 응용 프로그램을 사용하여 전문적으로 성장할 수 있는 기회를 제공해야하는 근본적인 이유이기도 합니다.
살바니니는 이 모든길에 우리와 동행했으며, 기계 조작자에서 프로그래머까지 모든 사람들이 교육과정에 참여했습니다.
이 모든 것들은 살바니니의 기술이 없었다면 할 수 없었습니다.
<살바니니 공식 유투브>
https://www.youtube.com/c/Salvagninigroup
Salvagnini
Salvagnini designs, manufactures, sells and services flexible systems for sheet metal working. With its complete and diversified range of machines, Salvagnini is able to intervene in countless application sectors, providing secure and innovative answers fo
www.youtube.com
살바니니에 대해 궁금하신 점이 있다면 위에 첨부한 공식 유투브나 사이트를 방문해주세요.
'Case Study' 카테고리의 다른 글
살바니니코리아 케이스스터디 - 그라다 사 (0) | 2022.10.13 |
---|---|
살바니니코리아 케이스스터디 - 테크란에스엘 사 (0) | 2022.10.13 |
살바니니코리아 케이스스터디 - 리사사 (0) | 2022.09.27 |
살바니니코리아 케이스스터디 - 마찌에리사 (0) | 2022.09.27 |
살바니니코리아 케이스스터디 - ICET사 (0) | 2022.09.14 |