판금 분야에서 50년 이상의 경험을 가진 회사가 혁신을 생각한다면 가장 먼저 고려해야 할 부분은 무엇일까요?
오늘은 2019년 자동 툴 교환 및 설정 장치를 포함, 다양한 옵션을 갖춘 살바니니 ROBOformER 로봇 벤딩 셀을 구입한 미네소타 지역의 볼타 만토바나(Volta Mantovana)의 BF Metal사를 소개해 드리겠습니다.
CEO인 안드레아 보셀리(Andrea Boselli)와 인터뷰를 통해 최첨단 자동화 시스템에 투자하게 된 이유를 알아보겠습니다.
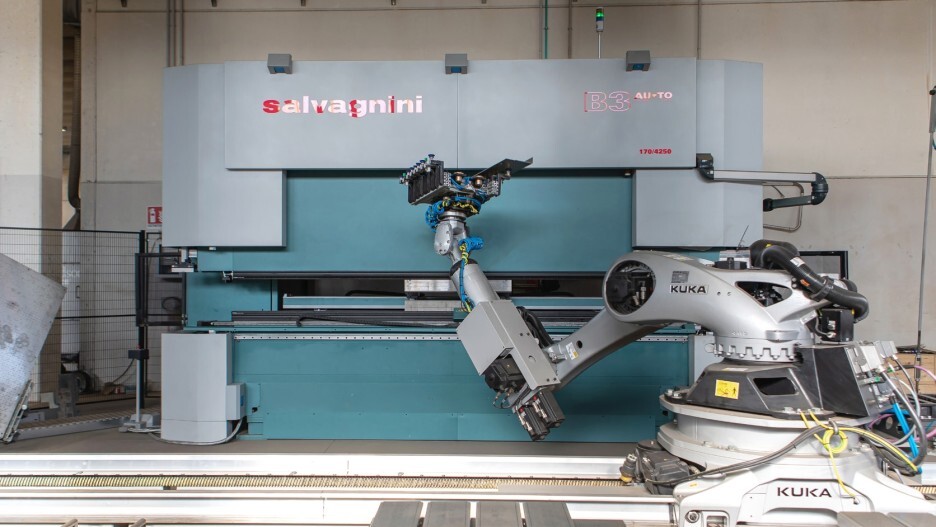
▶ 안녕하세요. 회사 소개 부탁드립니다.
회사는 1973년에 아버지에 의해 설립되었습니다. 저는 2000년에 입사했고 첫 번째 CO2 레이저 기계를 구입했습니다. 2011년에는 회사 이름을 공식적으로 BF Metal로 바꾸고 볼타 만토바나의 산업 지역에 위치한 현재 건물로 이전했습니다.
소유주 2명과 직원 8명으로 구성되었고, 특히 농업 및 자동차 산업에 종사합니다. 이것이 우리가 품질에 대한 관심이 높은 이유 중 하나입니다.
작업의 50%는 최대 5mm의 아연 도금 판금, 40%는 1~25mm 두께의 산세 강판, 그리고 나머지 10%는 알루미늄 또는 스테인리스 스틸입니다. 일반적으로 매달 약 150톤의 판금을 가공합니다.
ROBOformER 없이는 이 모든 것들이 불가능했을 것입니다. 관리 구매 및 판매에 종사하는 직원들과 오퍼레이터들의 지원으로 우리는 3개의 레이저, 5개의 기존 절곡기, ROBOformER 및 소형 로봇 셀을 직접 관리합니다. 또한 아버지 안젤로(Angelo)는 주로 기술 도면 작업을 하지만 그의 경험은 작업에 큰 도움이 됩니다.


▶ 자동화 도입 과정을 설명해주세요
2001년 볼로냐 무역 박람회에서 살바니니 레이저를 처음 접하였고 구매하였습니다.
그 이후 이 전에 일부 협력업체에 외주를 주었던 작업들을 다시 가져올 수 있게 되었습니다. 당시에는 자동화라는 개념이 생소했기 때문에 우리도 자동화에 투자하진 않았습니다.
두 번째 레이저에 투자하기로 결정한 것은 2011년 새 건물로의 이전과 동시에 이루어졌습니다. 우리는 4 x 2미터 레이저를 선택했습니다. 긴 사이클 타임을 고려하여 이번에도 자동화를 선택하지 않았습니다. 현재는 그 부분이 제일 아쉽다고 생각하기에 2016년 다른 레이저 시스템을 구입할 때는 살바니니와 상의하였고 로딩/언로딩 시스템이 장착된 스토어 타워를 추천받았습니다.
이번에는 100% 완벽한 선택이었습니다. 특히 레이저가 무인으로 작동할 수 있기에 야간 작업을 연장하면서 자율성을 높일 수 있었습니다. BF Metal이 선택한 솔루션은 작업 범위가 4000 x 2000mm이고, 4kW를 사용하여 분야, 재료 및 두께에 상관없이 사용할 수 있는 다용도 시스템인 L3 레이저입니다. 컴팩트한 스토어 타워와 결합된 자동 로딩/언로딩은 만토바 지역에서 충분히 경쟁력을 가질 수 있게 해주었습니다.
▶ 로봇 벤딩 셀 구매를 선택하게 된 계기가 무엇인가요?
2018년에 우리는 상당한 성장을 이뤘습니다. 자동차와 농업 분야에서 많은 주문을 받았고, 프레스 브레이크를 2~3개 더 구매하였습니다. 하지만 그에 맞는 인력을 구하는 것은 어려웠습니다.
우리는 자동화를 떠올렸지만 어떤 솔루션이 우리의 요구 사항을 잘 충족하는지 몰랐습니다. 자동 절곡기와 로봇 벤딩 셀 중에 무엇이 더 나을까요?
살바니니는 절곡 분야에서 방대한 경험을 가지고 있습니다. 수년간 프레스 브레이크를 이용해 생산 환경과 프로세스를 공유하는 다른 기계와 함께 사용해 왔으며, 로봇 벤딩 셀인 ROBOformER 개발을 전담하는 특정 부서인 Salvagnini Robotica 또한 존재합니다.
살바니니는 우리 부품을 분석하면서 사례 연구를 수행했고, 로봇 벤딩 셀이 우리에게 가장 이상적인 솔루션이라는 조언을 주었습니다.
처음에 우리는 로봇이 있는 B3 프레스 브레이크에 집중했지만 특별한 설정은 하지 않았습니다. 하지만 사용하면서 AU-TO 자동 툴 교환기에 관심이 갔고, 완전 자동화된 풀 옵션에 투자하게 되었습니다.
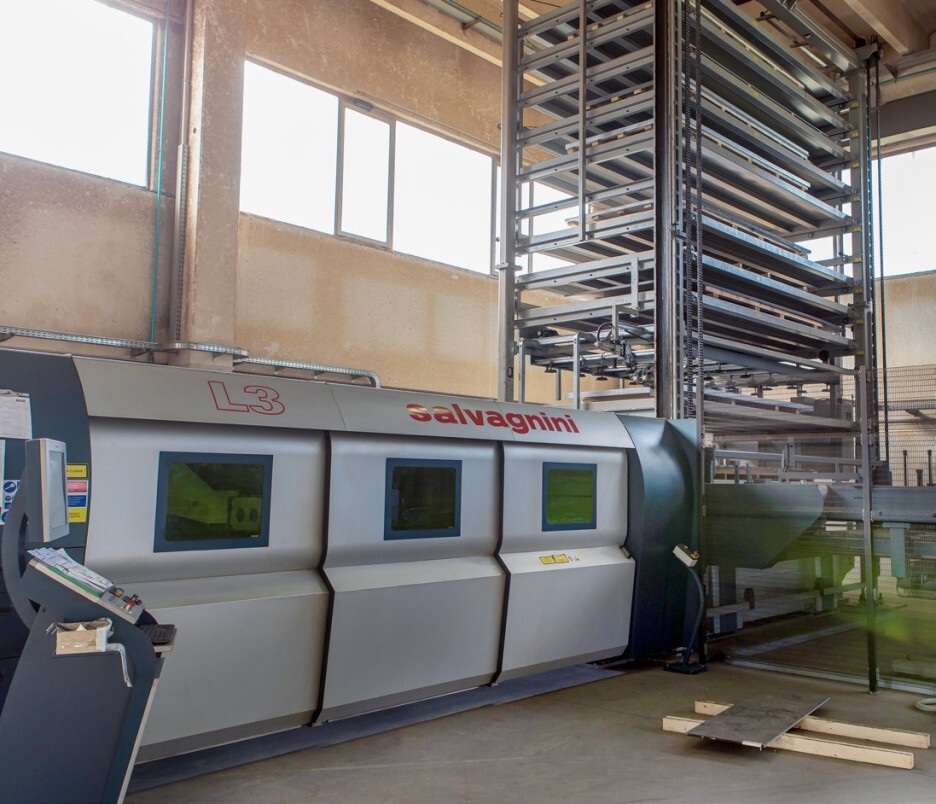
▶ 로봇 벤딩 셀 선택에 만족하시나요?
네. 완전히 만족합니다.
BF Metal에 설치된 ROBOformER는 ATA 및 AU-TO 장치가 있는 4250mm, 170톤 사양의 프레스 브레이크입니다. ATA는 절곡 툴 길이를 변경하고 자동으로 조정하여 생산 시간과 효율성을 재확보하며, AU-TO는 생산 흐름에 따라 툴을 자동으로 변경합니다. AU-TO는 설정 시간과 오류 위험을 줄이고 B3 프레스 브레이크의 가용성을 높입니다.
프레스 브레이크의 뒷부분에 위치한 툴 매거진에는 최대 24미터의 툴을 보관할 수 있습니다. 작업 부하에도 불구하고, 이전과 비교하여 배송 시간이 더 정확하고 신뢰할 수 있습니다.
ROBOformER를 사용하면 품질 향상 또한 가능한데, 프로그래밍이 완료되면 일관적인 절곡 품질을 보장합니다. 예를 들어, 제품 300개를 가공한다고 가정하면 항상 앙품 300개를 생산해냅니다.
또 다른 이점은 제품 공정에 있습니다. 2020년에 우리는 총 800,000개 이상의 부품을 생산했습니다. 우리 품목 중 일부는 한 달에 수천 개 단위로 생산되며, 이를 달성하려면 기존 프레스 브레이크가 2~3개 더 필요합니다. ROBOformER의 경우에는 재그립 없이도 자율적으로 부품을 생산합니다.
ROBOformER 구매는 회사의 생산 전략에도 변화를 주었습니다. 일반적으로 복잡한 60개 이상의 부품들은 로봇 벤딩 셀에서 가공되고, 더 작은 배치는 전통적인 프레스 브레이크로 작업합니다.
우리의 생산 계획은 가변적입니다. 하루에 여러 번 도구를 변경하거나 며칠 동안 동일한 설정을 사용하기도 합니다. AU-TO 공구 교환기는 이러한 가변성을 쉽게 관리합니다.
가동 중지 시간이 없으며 수동 재공구보다 훨씬 빠릅니다. 하루에 여러 번 공구를 교체하더라도 수동 프레스 브레이크에 비해 시간이 절약됩니다.


▶ 앞으로의 계획을 말해주세요
지난 2년간의 경험을 바탕으로 우리는 개편을 진행중에 있습니다.
우리는 절곡 부서 이전을 위한 새로운 작업장을 완공 중에 있습니다. 현재는 몇 가지 절단 기계를 보유중인데 그 외에도 2022년에는 레이저 장비에 더 많은 투자를 할 것입니다.
L3를 하나 더 구매하는 것을 계획 중인데 이것이 살바니니가 제공하는 서비스의 전반적인 가치를 증명하는 부분이라고 볼 수 있습니다.

<살바니니 공식 유투브>
https://www.youtube.com/c/Salvagninigroup
Salvagnini
Salvagnini designs, manufactures, sells and services flexible systems for sheet metal working. With its complete and diversified range of machines, Salvagnini is able to intervene in countless application sectors, providing secure and innovative answers fo
www.youtube.com
살바니니에 대해 궁금하신 점이 있다면 위에 첨부한 공식 유투브나 사이트를 방문해주세요.
'Case Study' 카테고리의 다른 글
[케이스스터디] Pompetravaini사 / 통합 프로세스로의 전환과 그 이점 (0) | 2023.01.06 |
---|---|
[케이스스터디] La Nordica사 / 단순한 제품이 아닌 고객 맞춤형 제품 생산 (0) | 2022.12.28 |
[케이스스터디] AKE 그룹 (0) | 2022.12.12 |
[케이스스터디] Mec.ti 사 (0) | 2022.12.09 |
[케이스스터디] Hefa사 / 냉장 캐비닛 산업에서의 성공 사례 (0) | 2022.12.08 |