차별화된 디자인과 품질을 위한 살바니니 장비투자
May 2023
이탈리아 산 조르지오 지역에 위치한 Studio 54사는 1994년부터 전문 냉장 장비를 생산해 왔습니다. 냉장고 캐비닛, 냉각기, 냉장 디스플레이, 바 장비 및 핫 디스플레이 케이스와 같은 표준 제품 외에도 맞춤 주문 제품을 제작합니다.
오늘은 이사이신 "마르코 브루세긴(Marco Bruseghin)씨"를 만나, 2022년에 자재 로딩/언로용 LTWS 스토어 타워를 갖춘 컴팩트한 구성의 살바니니 L5레이저를 재구매 하게 된 스토리에 대한 이야기를 나눴습니다.

▶ 꾸준한 성장을 이뤄온 배경은 무엇인가요?
처음 회사 설립할 때는 아주 작은 규모였기에 대부분의 인력은 디자인에 투자하였고, 생산의 80%를 외주로 작업하였습니다. 하지만 현재 우리는 63명의 직원과 함께 약 2,000만 유로의 매출을 달성하며 지속적으로 확장하고 있습니다.
회사의 성장과 함께 기술 투자 또한 이루어졌고, 현재 우리가 가진 살바니니 시스템은 L5 파이버 레이저 2대와 자동 로딩/언로딩 시스템, P4 자동절곡기 1대, 프레스 브레이크 3대입니다.
2019년, 우리는 창립 25주년을 맞아 웹사이트와 모든 제품 카탈로그를 업데이트 했습니다.
하지만 몇 달 후 코로나 19 팬데믹이 발생했고, 강제 휴업, 갑작스러운 생산 중단 등으로 어려움을 겪었습니다. 이때, 우리는 틈새 시장 중 하나인 병원 부문용 냉장 캐비닛 생산에 집중하였습니다.
그리고 2020년 여름, 우리는 본격적인 생산으로 돌아갔습니다. 케이터링 시장이 활기를 띠면서 갑작스러운 주문 증가로 인해 이전의 침체기를 회복할 수 있었습니다.
2021년에는 회사가 더욱 성장하였고 당시 회사 규모로는 이러한 성장세를 따라잡기 어려웠습니다. 특히 레이저는 이미 하루 18-20시간 가동되고 있었기에 우리는 교대를 통한 연중무휴 24시간 생산 또는 새로운 레이저 구입 중 한 가지 방식을 선택해야 했습니다.
사실 추가 직원을 뽑는 것이 어렵고, 작업실 공간도 부족했기에 어떤 선택도 쉽지는 않았습니다.
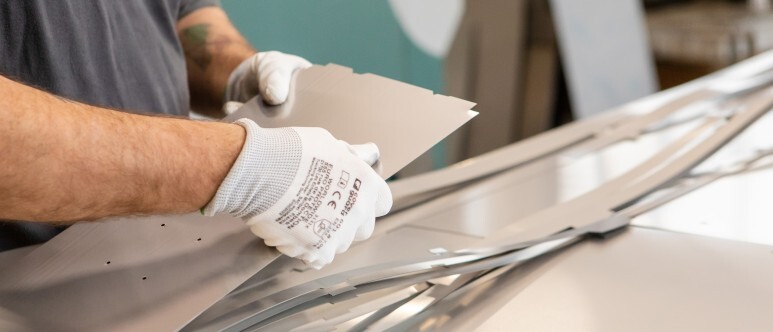
▶ Studio54의 선택은 무엇이었나요?
결국 우리의 선택은 새로운 레이저 시스템 구매였습니다.
이 과정에서 기존에 사용 중인 레이저와 동일한 구성이지만 더 컴팩트한 자동화 시스템을 선택하여 공간 문제를 해결할 수 있는 최적의 솔루션을 찾아냈습니다.
소재 자동 로딩/언로딩을 위한 컴팩트한 구성의 LTWS 스토어 타워는 작업자가 교대 근무를 시작할 때 소재 팩을 적재하고 생산을 시작하고, 끝나기 30분 전에 다시 적재하여 레이저를 통한 무인 생산 관리를 가능하게 했고, 가공 자율성 90%를 달성할 수 있었습니다.
우리는 대부분 자체 제품을 제작할 때는 주로 AISI 304 스테인리스강을 사용하지만, AOSO 430 및 아연도금강도 소량 사용합니다. 또한 대부분 2mm 두께를 넘지 않기 때문에 2kW 소스로 충분하였습니다. 보조 가스 선택과 관련하여 우리는 이미 사용 중인 가스를 재확인하였는데, 비용이 크게 증가한 것을 고려하여 이번에도 압축 공기를 이용한 ACUT 옵션을 선택하였습니다.
이 과정에서 두 장비 모두에서 사용할 수 있는 컴프레셔에 투자하였습니다. 따라서 현재 우리는 전체 부품의 95%, 전체 스테인리스강 생산량의 약 90%를 압축 공기로 절단하여 절단 품질을 유지하면서 가스 비용을 약 70% 절감하고 있습니다.

▶ 살바니니 장비는 문제없이 사용 중이신가요?
우리에게 있어서 전체 판금 가공 공정의 독점 파트너로 살바니니를 선택한 것은 탁월한 선택이었습니다. 프로그래밍은 절단 및 절곡 CAD/CAM을 포함하는 STREAM 프로그래밍 제품군을 사용하여 전적으로 사무실에서 이루어집니다.
올해는 새로운 ERP를 구매하여 디지털화 측면에서 더욱 확장하여 OPS의 모든 잠재력을 최대한 활용하는 것을 목표로 하고 있습니다.
또 향후에는 비효율적인 부분을 개선하고 가공 성능을 극대화할 수 있는 완전한 대화형 기계 및 소프트웨어 에코시스템을 구축하는 것을 목표로 하고 있습니다.
OPS의 역할은 ERP에서 받은 정보를 처리하고 STREAM에서 프로그램을 불러와 기계로 전송하는 생산 공정의 중심입니다.
OPS는 생산 목록을 실시간으로 업데이트하여 생산 변경으로 인한 혼란과 기계 가동 중단 시간을 줄이는 등 완전 자동화된 오류 없는 프로세스를 구현합니다.
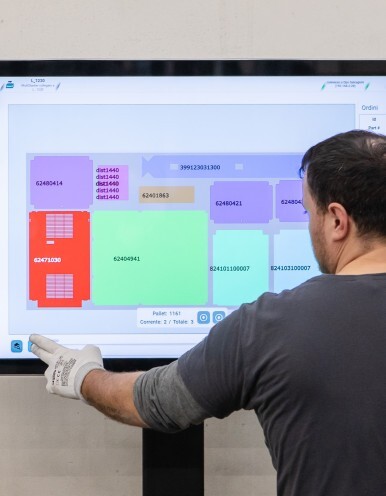

▶ 추후 계획을 말씀해주세요.
제가 생각하는 또 다른 핵심 과제는 생산 프로세스를 친환경적으로 만드는 것입니다. 최근 몇 년 동안 우리는 부품의 재활용 가능성과 관련하여 제품에 대한 연구와 노력을 기울여 왔습니다.
한편으로는 소비를 줄이고 재생 에너지원에 투자하며, 다른 한편으로는 환경에 미치는 영향을 줄이면서 제품을 더욱 친환경적으로 만드는 등 양방향으로 나아갈 의무가 있다고 생각합니다.
우리는 재료, 구성 요소, 기능 및 디자인에 대한 심도 있는 연구를 바탕으로 품질 측면에서도 지속적으로 개선하는 것을 목표로 합니다.
디지털화, 지속가능성, 품질이라는 세 가지 목표는 모두 밀접하게 연결되어 있으며, 우리만의 차별화된 디자인과 품질을 찾기 위해 더욱 집중할 계획입니다.
<살바니니 공식 유투브>
https://www.youtube.com/c/Salvagninigroup
Salvagnini
Salvagnini designs, manufactures, sells and services flexible systems for sheet metal working. With its complete and diversified range of machines, Salvagnini is able to intervene in countless application sectors, providing secure and innovative answers fo
www.youtube.com
살바니니에 대해 궁금하신 점이 있다면 위에 첨부한 공식 유투브나 사이트를 방문해주세요.
'Case Study' 카테고리의 다른 글
[케이스스터디] Industrial Laborum사 / 살바니니 장비를 활용한 생산 전략 변경 (0) | 2023.08.25 |
---|---|
[케이스스터디] Ferrero사 / 살바니니 장비 구매로 이룬 제품 생산 내재화 (0) | 2023.08.18 |
[케이스스터디] Luoyang Hefeng사 / 철제가구 산업에서의 살바니니 자동 절곡기 (0) | 2023.07.21 |
[케이스스터디] Kögel사 / 살바니니, 자동화된 일체형 라인 구축을 위한 투자(2) (0) | 2023.07.06 |
[케이스스터디] Kögel사 / 살바니니, 자동화된 일체형 라인 구축을 위한 투자(1) (0) | 2023.06.29 |